CleanAir’s Performance Group regularly provides the power and process industries with water flow rate evaluations through a variety of direct measurement techniques.
Pitot Tube Flow Rate Measurements
Water flow rate measurements with a calibrated Pitot tube are best made in pipes at a point that there is a well-developed flow profile. As such, flow rates are typically measured in pipes that have at least six pipe diameters of straight length from a flow obstruction or bend. Flow rates can be measured in pipes as small as 4 inches to over 20 ft in diameter. Typically, two mutually perpendicular 20-point traverses are made to obtain the average velocity in the pipe. The flow rate is calculated from the product of the average velocity and the cross-sectional area in which the traverses are conducted. Access to the flow is made through full port ball or gate valves. Please contact CleanAir for guidance regarding pitot tap size and placement to ensure the accuracy of pitot tube flow rate measurements.
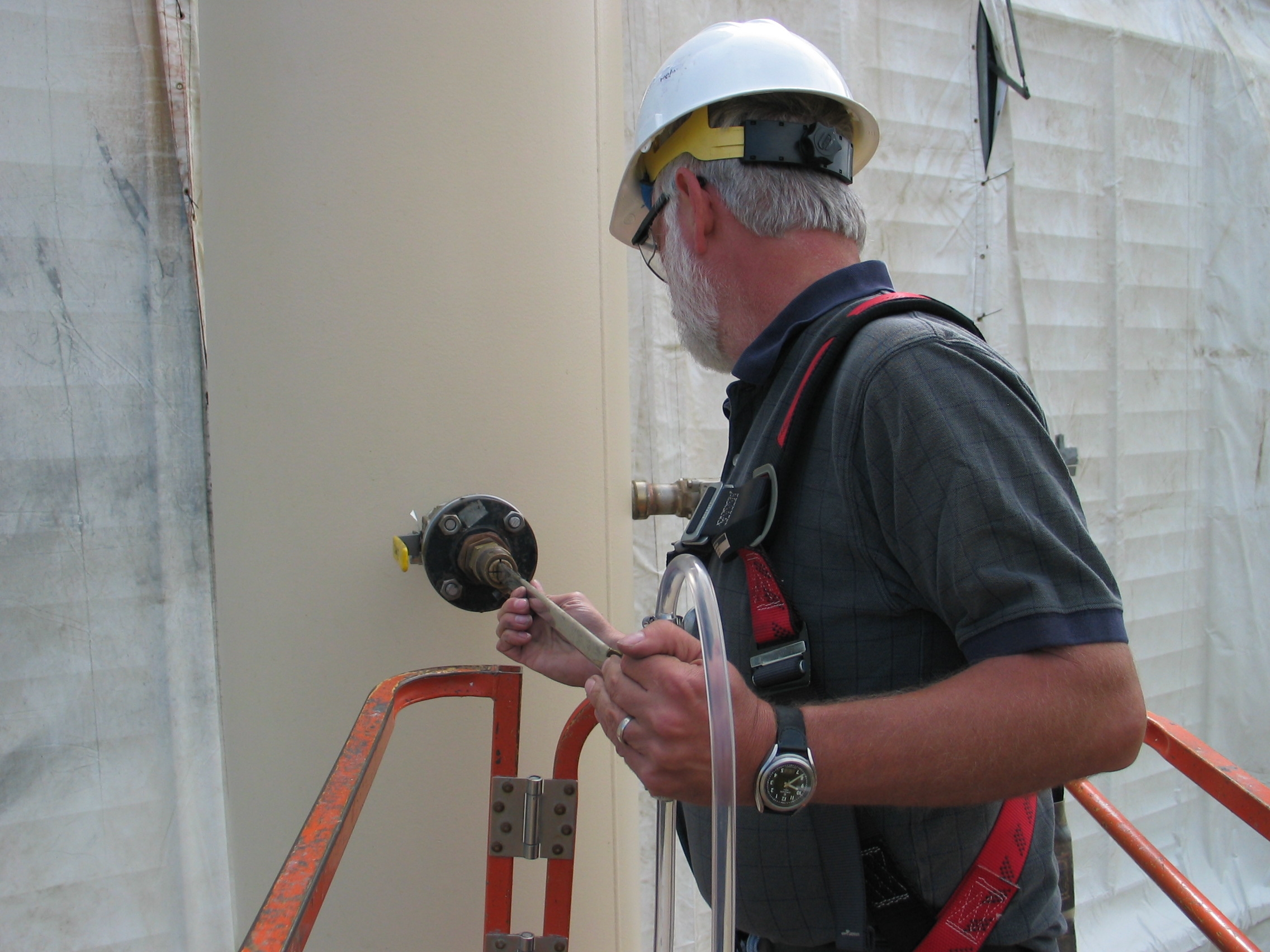
Dye Dilution Flow Rate Measurements
In applications where pitot taps cannot be installed in a straight run of pipe, dye-dilution flow rate techniques may be a viable alternative. Dye-dilution flow measurements are especially well suited for “once-through” applications to determine pump, condenser, or helper cooling tower flow rates. The flow rate accuracy does not depend on pipe cleanliness, pipe geometry or turbulence at the measurement point and flow measurements can typically be performed with existing taps. In this technique, fluorescing Rhodamine WT dye is introduced at a precisely known injection rate into the flow stream under investigation. At a downstream location after the dye is thoroughly mixed, the concentration of the dye in the system water is measured with a calibrated fluorometer. The downstream concentration is proportional to the mass flow rate of the water. The accuracy of the dye dilution technique is dependent on uniform mixing of the injected dye at the sampling point. This usually requires from 40 to 100 pipe diameters of pipe between the injection and sampling points. If adequate mixing can be accomplished, accuracies of less than two percent can be achieved using this method.
Ultrasonic Flow Rate Measurements
In closed loop applications where pipe taps cannot be installed, a strap-on ultrasonic flow rate measurement may be an option. Ultrasonic flow rate measurement accuracy is a function of flow profile, pipe material of construction, pipe thickness and homogeneity. Ultrasonic flow rate measurements are best made in new or clean steel pipe with long straight runs to ensure well developed velocity profiles. Ultrasonic flow rate measurements are sometimes used to complement other flow rate measurements for test programs when an increased uncertainty in the smaller flow rates does not detract from the test objective. For example, ultrasonic flow rates may be used to quantify auxiliary flows around a steam condenser when the main condenser flow is measured via dye-dilution or the make up into a cooling tower cold water basin where the tower water supply is measured via pitot tube traverse of the hot water risers.